Introduction of fused zirconia corundum brick products
The use of industrial zirconia, alumina as raw material, through the ultra-fine grinding, and strictly control the particle size, with conventional technology, can be made of high strength, high toughness of zirconia-alumina composite ceramic, is a high-grade refractory materials.
The results show that the addition of alumina in the zirconia matrix can effectively inhibit the growth of zirconia grains, which is beneficial to the existence of metastable tetragonal phase of zirconium oxide grains, so as to improve the strength and fracture toughness of the materials. When the mass fraction of alumina is 20%, the flexural strength of the composite ceramic reaches 676.7MPa and the fracture toughness reaches 10MPa / m2. Phase transformation toughening and particle dispersion toughening effect are superimposed on each other to improve the mechanical properties of composite ceramic materials.
The alumina powder was prepared by thermal decomposition method. The zirconia ultrafine powder was prepared by chemical coprecipitation method. The zirconia / alumina composite ceramics were prepared by the appropriate process. It is believed that the addition of alumina can inhibit the growth of zirconia grains and improve the strength and toughness of the matrix. When the mass fraction of alumina reached 30%, the flexural strength of the yesterday ceramic fired at 1600 ℃ was 968MPa and the fracture toughness was 13.7MPa / cm2.
In the corundum refractory by adding zirconia, made of jade - zirconia composite material, which is phase change strengthening, toughening and microcracking toughening theory in the application of refractory examples. Corundum - zirconia samples undergoes phase transition during calcination, and a certain amount of microcracks are formed inside the material, which is beneficial to the increase of mechanical strength and toughness. When the amount of zirconia is less, the number of microcracks in the material is small, which has little effect on the strength of corundum refractory. When the exhaled amount is too high (such as above the mass fraction of 9%), The number of cracks is more, resulting in the material's flexural strength decreased.
With corundum, synthetic mullite and monoclinic zirconia as raw materials, with the material with isostatic pressing, in 1650 ~ 1700 ℃ firing. The law of the flexural strength of the specimen changes with the temperature: the intensity increases first and then increases with the temperature, and then decreases with the temperature after the turning temperature, which is due to the thermal expansion mismatch between the different crystal phases and the local cohesion of the microcrack the result of. Turning temperature of 800 ~ 900 ℃, due to zirconia martensitic transformation, in the 1000 ~ 1200 ℃ have "valley" characteristics, the bottom at 1100 ℃.
The addition of zirconia has a significant effect on the high temperature mechanical properties and microstructure of the sample. In the low temperature stage (20 ~ 800 ℃), the strength change after adding zirconia depends on the two factors of microstructure - structural skeleton strength and microcrack density, generally the latter. When zirconium oxide is about 15%, the uniformly dispersed zirconia is filled in the corundum-mullite skeleton, and some of the strengthening effect is due to the weakening effect caused by the microcracks produced by the martensitic transformation. , So the strength is reduced. When the amount of zirconia increases to 20% ~ 35%, the structural skeleton is weakened, and the microcrack density increases, so the strength continues to decrease. Valve by zirconium to reach more than 40%, structural skeleton strength has improved significantly, so the strength of a slight rebound.
In the 1300 ~ 1500 ℃ high temperature stage, most of the microcracks have been bridged and passivated, so the reinforcement has little effect. At this time to determine the strength of the structural skeleton strength and grain boundary solid solution strengthening effect. With the addition of zirconia to increase the grain boundary solid solution strength effect increases, there are a small amount of zirconia may enter the grain boundary glass phase, can improve the viscosity, but also play a certain role in strengthening.
In zirconia toughened alumina ceramics, zirconia particles are introduced by mechanical mixing. In the sintering process, the two substances do not react or compound, but at high temperature by surface evaporation and diffusion and interface diffusion and cloak to densification, are solid-phase sintering. The addition of zirconia has the effect of promoting sintering, and when the sintering time is prolonged, it can hinder the growth of alumina grains and improve the high temperature mechanical properties of the products.
2% titanium dioxide is added to zirconia corundum. Titanium dioxide takes precedence with zirconia to form solid melt. However, the formation of melt does not prevent the crystal transition of zirconia. The zirconia is still present as m-ZrO2 as the main crystal phase. Titanium dioxide promotes the development of alumina and zirconia grains, which increases the porosity of the material and decreases the strength. The addition of titanium dioxide reduces the high temperature thermal expansion of zirconia corundum, but the coefficient of thermal expansion is not a uniform linear relationship with the temperature, and the maximum value occurs at 1100 ° C.
The addition of zirconia in alumina ceramics to produce alumina / zirconia sintered materials has been paid much attention in recent years due to its excellent mechanical and thermodynamic properties. The series of ceramic materials, high hardness, good toughness, excellent wear resistance. Can be used to manufacture cutting tools, plug, sliding bearings. In the metallurgical industry as a sliding nozzle skateboard material. A series of theoretical studies on alumina-zirconia materials have also laid a good foundation for the manufacture of high quality Al2O3-ZrO2-C materials.
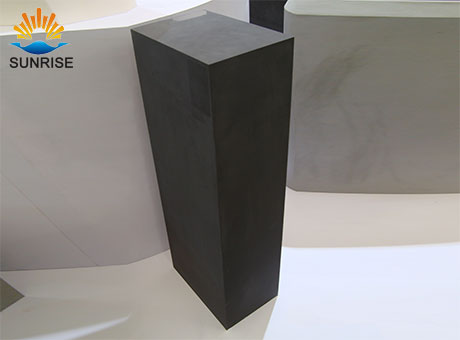
Read more