Lightweight and heavy composite thermal insulation brick for ladle
The heavy part of the light and heavy composite thermal insulation bricks used for the permanent lining of the refined ladle is equivalent to a high-alumina brick, and the light-weight part is equivalent to a clay-based thermal insulation brick. It has been shown that light and heavy composite insulation bricks are used for the permanent lining of ladle, which has obvious energy-saving effects and can achieve significant social and economic benefits.
The heavy part of the composite brick mainly serves as a safety lining to prevent the occurrence of an accident when the ladle working liner is worn through. In the past, most of the steel mills used a clay brick as a permanent lining. In the aluminum silicate refractories, the alumina content and the apparent porosity of the product are the decisive factors affecting the slag resistance. The alumina increases, the slag resistance increases, the apparent porosity decreases, and the slag resistance improves at the alumina content. Among these two factors of apparent porosity, the apparent porosity has the most obvious effect on the slag resistance of products.
Therefore, the use of high aluminum as the material for heavy parts compensates for the lack of clay bricks used as safety linings. The slag resistance test was carried out using high alumina and made of 65% coke, 15% primary bauxite and 20% clay. Steel slag is an oxidizing slag for the smelting of bearing steels. The test temperature is 1400°C. Considering the firm combination between economical, light and heavy qualities, it is feasible to use chemicals whose composition is close to that of clay. The light part requires good heat insulation and the thermal conductivity should be ≤ 0.5W (M·K).
The raw materials used in light and heavy composite thermal insulation drills are bauxite clinker grade 1, bauxite clinker grade 2, porous clay clinker, porous bauxite clinker, float beads, clay binder and additives.
Physical and chemical properties of lightweight composite heat-insulating firebrick: physical and chemical properties of the light part: Al2O3 ≥ 45.89%, Fe2O3 ≤ 2.46%, bulk density ≤ 1.2g/cm3, ambient temperature compressive strength ≥ 4.08MPa, refractoriness ≥ 1670°C , Thermal conductivity (350 °C) ≤ 0.438W (M · K); heavy part of the physical and chemical properties: Al2O3 ≥ 63.44% Fe2O3 ≤ 1.58%, normal temperature compressive strength ≥ 35.0 MPa, refractoriness ≥ 1790 °C.
In addition to being used as a permanent lining for refining bags, light and heavy composite thermal insulation bricks can be used as safety insulation lining materials for other thermal kiln furnaces, and also used as lining and masonry materials in thermal equipment of building materials, electronics and chemical industries. The application is very extensive.
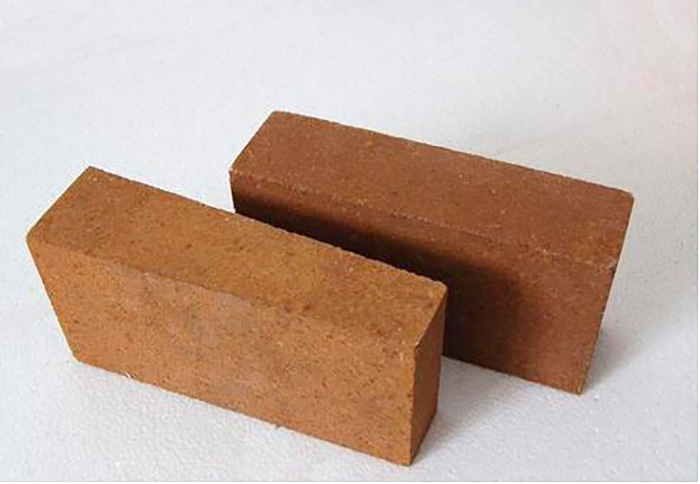
Read more