The nature of mullite refractory bricks determines its role
The firebrick made of sintered or fused mullite as the main raw material may be entirely made of mullite, partly may be mullite, and some may be made of corundum. The former became mullite refractory bricks, and the latter was called corundum mullite refractory brick or corundum mullite brick. The production process of mullite refractory bricks is the same as that of high-alumina bricks. The ingredients are mixed, formed, dried and fired. The firing temperature is related to the composition of the ingredients, the purity of the raw materials and the requirements for the performance of the firebrick, and is usually 1500 to 1700°C.
Mullite refractory bricks and corundum mullite bricks have the advantages of high load softening temperature, low high temperature creep rate, and good thermal shock resistance. They are widely used in hot blast stoves, glass melting furnaces, CDQ and heating furnaces and other industries. On the furnace. Mullite refractory bricks are easily attacked by alkaline fire bricks at high temperatures. In addition, at high temperatures, mullite can be damaged by reaction with water vapor to form Al2O3.
Therefore, mullite refractory bricks should not be used for long-term use in high-alkaline slag and high water vapor content environments.
In addition to mullite and its composite refractory firebricks with corundum, mullite can also be constructed with other materials to improve its properties such as zirconium mullite refractory bricks, mullite-silicon carbide firebricks and so on. The so-called zircon mullite refractory bricks are mullite-zirconia composites. However, due to the high price of zirconia, in practical production, zirconium mullite clinker or refractory bricks are often produced by reacting Al2O3 or bauxite with zircon.
Such firebricks and raw material manufacturing methods include fused and sintered methods. The fused cast aluminum-zirconium-silicon (AZS) firebrick is prepared by calcining Al2O3 and ZrSiO4 ingredients to obtain zirconium mullite clinker, and then crushing, kneading, forming and firing to obtain zirconium mullite refractory bricks. That is sintered AZS bricks.
When using bauxite as a raw material, the most common is to introduce ZrSiO4 into high alumina bricks to improve the thermal shock resistance of high alumina bricks, the so-called "anti-stripping high alumina bricks." The ZrO2 produced by the reaction is dispersed in mullite and corundum. Due to the phase change of ZrO2 during heating and cooling, micro-cracking occurs around the ZrO2 particles, thereby improving its thermal shock resistance. Sintered AZS refractory bricks are commonly used in glass kilns.
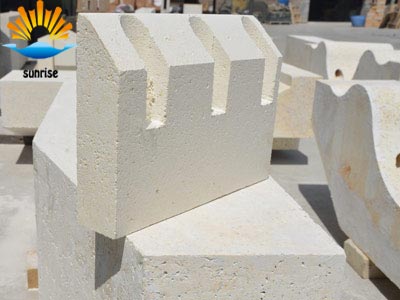
Read more