Casting Methods For Manufacturing Fused Cast AZS Blocks
In general, alumina-zirconia-silica electrofused cast refractories are referred to as fused Cast AZS blocks. Fused Cast AZS blocks are the most widely used materials both in glass contact and superstructure of glass melting furnaces.
Fused cast AZS blocks are manufactured by fusing or melting a blended raw material of plural composition in an electric furnace, casting the fused or melted material in a mold, and then gradually cooling (annealing) the cast product in alumina powder. High density, small or large shapes are obtained. When appropriate, a finish is made by grinding with diamond tools.
There are four casting methods to manufacture fused cast AZS blocks: Normal casting(PT), Tilt casting(QX), Semi-Void-Free casting(ZWS), and Void-free casting(WS).
Normal casting(PT)
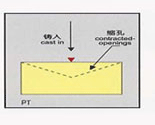
It is the general casting method. Due to volume shrinkage from liquid-solid transform and rapid solidification of a casting ,normal cast blocks have cavities located under the filling scar. The feasible limits of cavity can be evaluated and indicated by the volume-weight testing of blocks in-situ according to the technical specifications. It is used for upper structure of the glass melter and work pool, also the parts in contact to glass with low temperature.
Tilt casting(QX)
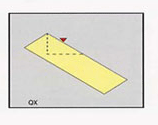
Fused cast AZS blocks manufactured in this method have casting cavity on the lower back face of the brick, and the other end is entirely compacted. The feasible limits of cavity can be evaluated and indicated by the volume-weight testing of blocks in-situ according to the technical specifications. Meanwhile, blocks which height less than 900mm are not suitable to be manufactured by this process. When being used, the compacted part is upward, while the casting nozzle is outward. They are mainly used in the wall of melting tank and work pool.
Semi-Void-Free casting(ZWS)
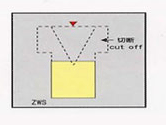
It is similar with WS. While casting, the casting size is bigger than it is required. There are a few shrinkage cavities left at the end of the block after the header cutting. Block evaluation in-situ begins from the determination for the feasible size and deepness of cavity remainder at first and then to the volume-weight testing of blocks according to the technical specifications. When being used, the end of shrinkage cavity is downward, the other end is upward. It is most used in side wall.
Void-free casting(WS)
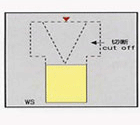
In the process, additional liquid from the header fills sufficiently into a casting. The casting size is bigger than that is required. The shrinkage cavities are in the upper head, and will be cut after annealing. Therefore the left is free of casting cavities and it is compacted very much. Block evaluation in-situ includes the acceptance or rejection for somewhat trace of cavity remainder which perhaps appeared and the volume-weight testing of blocks according to technical specifications. When being used, the end of cast is downward, and the other end is upward. It is mainly used at wall bottom,dog hole, discharge home, manifold and main parts of melting tank.
Zhengzhou Sunrise Refractory Co., Ltd. offers different types of
fused cast AZS blocks in different shapes and sizes, including Fused Cast AZS 33#, Fused Cast AZS 36# and Fused Cast AZS 41#.
Read more