Refractory Selection For Oxy-Fuel Glass Furnace
Oxy-fuel glass furnace can save fuel, reduce pollution, improve glass quality and raise the output of the furnaces. It is widely used for the production of special glass and float glass. However, the increase of large amounts of alkali vapor and water vapor in the oxy-fuel glass furnace enhances the corrosion of refractory materials. Therefore, the oxy-fuel glass furnace has a higher requirement for refractory materials.
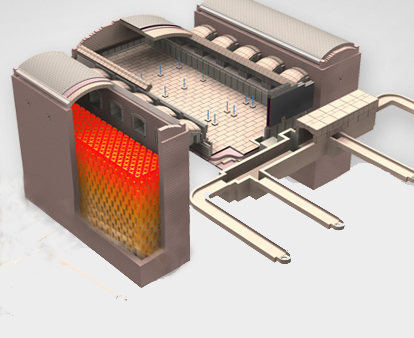
In the oxy-fuel glass furnace, fused cast AZS block is always used in the breast wall. The flame causes mechanical erosion in the breast wall. The hot air causes the flying of alkali components. Na2O and K2O are adhered to the surface of the breast wall and react with some compositions of breast wall bricks. Besides, alkali vapor diffuses into the bricks through gaps and open pores and causes chemical erosion. The gas in the brick extrudes the liquid phase out and enhances the spalling of bricks. In order to reduce the corrosion of fused cast AZS, some things should done to improve its performance, such as reducing the glass phase and improving its creep resistance.
The crown traditionally employs silica brick. The silica brick is cheap and has high refractoriness under load. When used as the crown, the surface of the brick will be corroded by the alkali components and form new glass phase rich in SiO2. The new glass phase has a high viscosity and will block the pores and prevents the in-diffusion of the alkali component into the inside of the bricks. The crystalline transformation caused by the temperature changes causes volume changes. In the oxy-fuel glass furnace, the temperature of the crown surface is lower than that in air-fuel glass furnace, but the concentration of alkali vapor is higher. All these factors enhance the corrosion of silica bricks. α-β
fused cast alumina block and low exudation fused cast AZS are more suitable for the crown of the oxy-fuel glass furnace. β fused cast alumina block is also used in the crown.
The sidewall of the oxy-fuel glass furnace also employs fused cast AZS block. The glass phase of AZS is easy to exude at high temperature and the crystal phases of AZS are isolated and drop into the glass melt due to gravity. The alkali oxides such as Na2O and K2O in the glass melt react with the Al2O3 in the bricks, which will produce Nepheline and β-Al2O3. The ZrO2 and Al2O3 in the brick is separated out to the surface of the brick and form a protective layer to prevent the further corrosion.
Although fused cast AZS and fused cast alumina block have higher corrosion resistance than other refractories, they still suffer from severe corrosion. Therefore, low exudation fused cast AZS block, specific fused cast alumina block and high quality silica brick are developed for different demanding parts of the oxy-fuel glass furnaces.
Read more