How To Select High Alumina Brick For The Glass Furnace
High alumina brick is a type of silicate refractory that contains more than 48% alumina. It is made of high-quality bauxite clicker as starting material by molding at high pressure and sintering at high temperature. It is mainly used in the glass furnace.
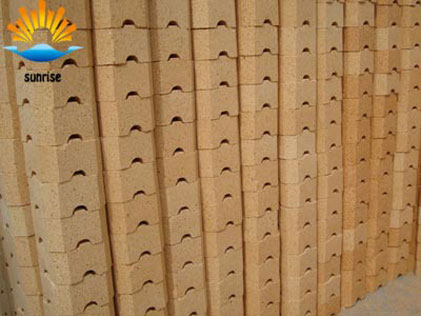
According to the content of Al2O3, high alumina brick can be divided into 3 grades:Ⅰ(Al2O3>75%),Ⅱ(60%-75% Al2O3) and Ⅲ(48%-60% Al2O3). According to the mineral composition, it can be divided into low mullite, mullite, mullite-corundum, corundum-mullite and corundum.
Poor quality high alumina brick will not only cause frequent shutdown of the furnace, limit the melting temperature and reduce the production capacity, but also shorten its service life.
When selecting high alumina block for the glass furnace, consider the type of the furnace, the type of glass and fuel, the parts used and the operating environment. High alumina brick used for the glass furnace should have good resistance to the molten glass, slags and gaseous substances and thermal stability.
Check the specifications and dimensions of the bricks and observe the appearance. High quality high alumina brick has smooth surface, light yellow or white color, flat sides, no broken edges and angles and no cracks.
The thickness of the surface debris of iron and calcium should be not more than o.5mm. The area of the debris should not exceed 20% of the total area. The erosion depth of the low-melting materials should not exceed 5mm.
A single Ⅰgrade high alumina brick weighs 4.5kg, Ⅱ grade brick 4.2kg and Ⅲ grade 3.9kg.
High alumina brick can be used in the high temperature areas of the glass furnace. Low porosity high alumina brick can be applied to regenerators, high temperature areas, feeder chutes and some glass-contact areas. Bricks with appropriate porosity have good thermal shock and can be used in the superstructure of the forehearths.
Read more